
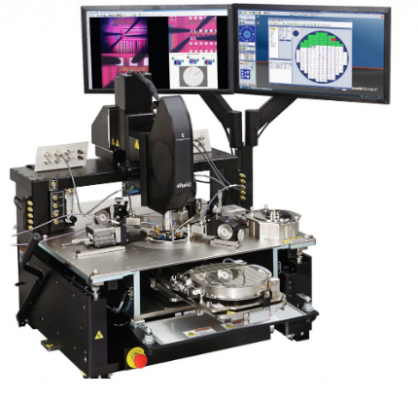
The SolidCAM simulator provides so much more detail and is much easier to access - Simulation in Esprit is very slow.
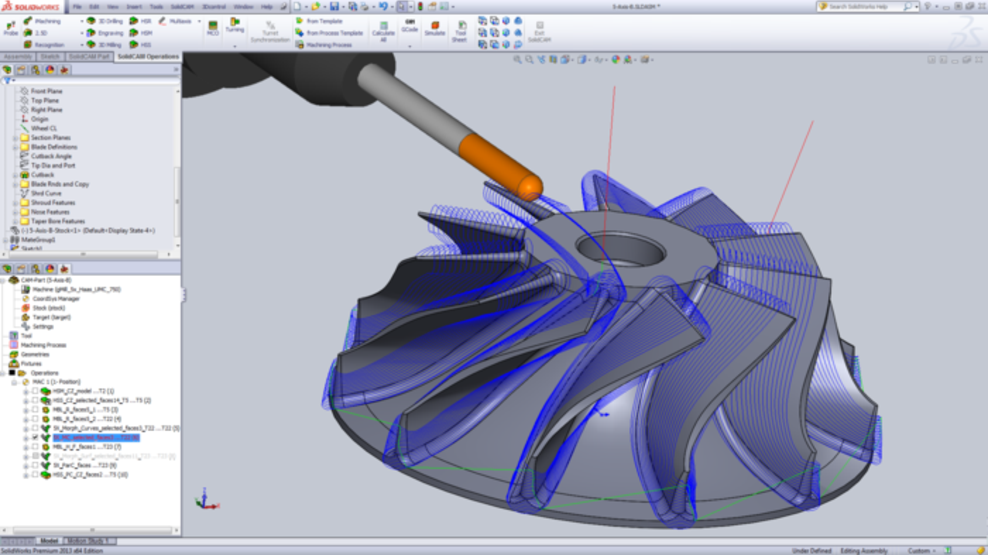
See this presentation on iMachining vs so-called competitors: T hat takes away the guesswork in setting the cutting conditions - a major advantage to all machinists - the more experienced and the less experienced. Also, iMachining has the amazing iMachining Wizard that automatically calculates optimal feeds and speeds, for every point of the toolpath, taking into account the stock material properties, cutting tool type, and machine tool parameters. SolidCAM's iMachining is far more superior to Esprit's Profit Milling - the iMachining module maintains constant tool load, by varying the feed according to the cutting angle, generating efficient morphed spiral and trochoidal tool paths, where machining time is drastically reduced (70% and more), and tool life is dramatically increased (5 times and more).Integration into SolidWorks provides toolpath associativity - so if a model changes, all toolpaths are automatically updated.In Esprit, importing models sometimes creates issues where models lose integrity and needed “workarounds” to create tool paths in affected areas.Esprit has no integration to SolidWorks - SolidCAM is seamlessly integrated in Solidworks:.More info on each individual peice will be available soon. Example: choose a HSK 50 spindle for roughing and semi-finishing, and a 80,000 rpm air bearing spindle to produce amazing surface finishes. Our Z2 machines allow daul spindles to be fully integrated into the machine. Each part is straight off the Röders with no poshling.Īll test cut pieces were milled using a 80,000 rpm spindle with a 10th of a micron step-over. Röders has dominated the optics industry ever since our advanced RMS6 control found it's perfect match with linear motor technology. Admiring the lastest test cuts sent to us from the Röders test cut facility in Soltau, Germany.
